Stiffness tests
Photo by Alessandro Trovati
We are delighted to finally publish the third part of The RouesArtisanales 2008 great wheel test focusing on stiffness – a somewhat hazy and complicated concept.
Wheel stiffness indicates deflection of the rim as a result rider weight and strength. Higher stiffness generally brings better performance. However, is maximum stiffness always
necessary? What happens if a wheel’s not stiff enough? How much deformation can actually be perceived by the rider?
We will do our best to answer these questions in what follows.
Wheels are subject to numerous strains. First of all, they are subject to the rider’s weight when he rides. Second, they are subjected to lateral loads when he stands on the pedals. Third, the rear wheel has to transfer torque to the road, and finally it has to resist potholes and other road irregularities. In response to all these loads, the hoops deform laterally and
radially to some degree.
Frontal stiffness
1a) The frontal stiffness – Preview
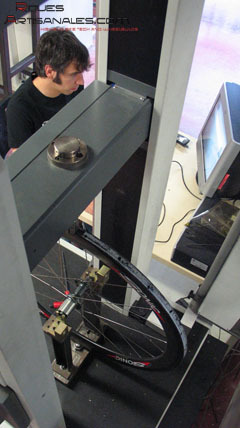
Frontal stiffness test @Mavic par Thibaut Montagnoni
Wheels’ frontal stiffness is extremely high and studying lateral stiffness will provide much more useful insights. The vertical deformations reached are out of range for us mere mortals. A standard wheel has frontal stiffness of 1500-2500N/mm for example: that’s to say that it takes 150-250kg to deform the wheel by a single millimeter. We have kept the data in our spreadsheets waiting for some newer technologies to be launched when frontal stiffness could conceivably become a factor in overall wheel comfort. The current wheel structure (rim, hubs, laced together with spokes under tension), does not really allow comfort. Only a few wheels whose structure is very special, would
eventually reduce the vibrations. The following wheels may be among them: the ADA made by Cees Beers have full Kevlar spokes, the Spinergy Stealth PBO whose spokes are
made out of Zylon fibres may bring a touch of softness (although the deep rim and tensioned spokes bode against it), and Lew Racing Pro VT-1 which does not have tensioned
their spokes, deform easily (frontal stiffness of 800N/mm which is 1mm of deformation under 80kg of load.
Even though some wheels seem, a priori, softer than others, the comfort will mostly be related to the tyre:
– tubular or clincher
– inflation pressure of the tyre
– tyre width
– supplness of the casing
– suppleness of the inner tube
Thus, high-end handmade tubulars generally provide better comfort than clinchers. Their casing is supple and light thanks to the materials used, such as cotton or silk. A latex inner
tube is fitted in most cases which is softer and more resistant than standard butyl. Moreover, their structure favours the performance and feeling on the road. Veloflex, FMB and Dugast are all famous for their high end tubulars and Vittoria to a lesser extent. Continental prioritises puncture resistance over casing suppleness and therefore ride quality.
Coming back to our frontal stiffness test, the wheel is fixed by its axle, then crushed. The force applied is determined by software which records deformation at the same time.
The wheels deform very little because of several parameters playing an important role in the vertical deformation. The rim height and its high frontal stiffness are not really prone to deform easily. Shallower rims obviously deform more easily than deep rims because they are not as stiff. The spokes also play a role: their number, crossing pattern, tension and spoke stiffness (material, cross section) all have an influence on overall vertical stiffness of the wheel. A low cross section spoke with low spoke tension will deform or lose its stiffness quicker than a high cross section and high tensioned spoke. The hub plays a role too, but its influence will be smaller than the two first.
Finally, rear wheels are not as stiff as front wheels because of the bracing angle difference on the two sides of the rear wheel.
1b) The frontal stiffness – Summary
As summary, a rear wheel with a shallow rim, with low tensioned spokes, will vertically be easier to deform than a deep rim wheel with high tensioned spokes. The deformation is about 1mm per 140kg (rear Lightweight, rear Sonic 50mm, rear Speedcomposites), to 1mm per 200kg (front Mavic CCU, front Corima Aéro, etc) or 1mm per 260kg (front Zipp 404, Lightweight front).
Nevertheless, there are a few special cases worth highlighting:
– The first exception concerns the Shimano 7850 C24TU and C50TU wheels, but also the Mavic Cosmic Carbone Ultimate offering higher frontal stiffness front than rear. The high spokes tension seem to be responsible of this phenomenon: the frontal stiffness are 2850N/mm front to 2940N/mm rear for the C50, and 1790N/mm front to 1840N/mm rear for the C24. The CCU also follows this special case: the front is 1910N/mm and the rear is 1970N/mm. Of course these figures will vary slightly between wheelsets with the spoke tension, the rim manufacturing batch, etc.
– The second exception is the Lew Racing Pro VT-1. They offer a very high frontal deformation: 75 to 80kg create a deformation of 1mm in spite of the 46mm deep rim. The spokes bonded to the hub and to the rim have no tension. The vertical loads deform the wheel shape and the spokes bend, which certainly explains a part of the weight limit, but also the pleasant and unusual ride qualities. The deformation is visible on this picture:
Lateral stiffness
2a) The lateral stiffness – Explanation
Lateral stiffness is the biggest and most complicated part of the Great Wheel Test. This is why we’ve taken so long to get this article online!
Lateral stiffness is an important and complicated parameter from a performance point of view. Unless we can equip a bike with several power sensors, and perform a long series of tests,
it is difficult to measure any gain or loss from laterally stiff or flexy wheels.
Jean-Pierre Mercat, engineer from Mavic, has researched the subject extensively: « We performed tests with SRM and hearth rate to study the output power in ascending sessions, with four visually identical wheels of different lateral stiffness (from 20N/mm to 80N/mm).
We did not have serious conclusion, despite 300 tests: there were no performance difference at moderate powers: from 180W to 350W. However, when climbing at full power, with Elite racers,
the conclusions were quite different. The maximal power reached was lower (-150W at 1000W) with the flexy wheels at 20N/mm, but there were no difference between 60 and 80N/mm. About the m
aximal hearth rate, it was lower with the least stiff wheels than with super stiff wheels. The power potential is somewhat absorbed by the flexibility and the acceleration is not as
rough. »
This is significant. Lateral stiffness is important for sharp accelerations or sprints, which are regularly encountered during races.
We also did some tests during races using a Powertap powermeter which has an error margin of 1.5%. The average power in breakaways of normal road races (power in criteriums are higher) were around 300W for the first hour falling to 270W after two and a half hours. Power output during accelerations were between 500-700W for a few seconds, while sprints often required 1000-1300W. The stiff wheels are obviously beneficial here.
2b) The lateral stiffness – Protocol
Lateral stiffness is tested by loading the rim of a wheel from the side – on the weaker drive side for the rear wheel – and recording rim deflection at this spot, and on the opposite side.
Depending on the load and the deformation, the stiffness in N/mm can be calculed. The load used in the lateral stiffness test represent the rider weight: when the cyclist stands on the bike, his bike is not perpendicular to the ground, it is slightly angled. This angle create a lateral load on the rim (see the drawing above).
Beside this, when the rider pushes the pedals, the torque transmited through the spokes deforms the wheel because of the bracing angles creating a lateral component: even when sitting in the saddle, the rear wheels moves between the brake pads when a rider stomps on the pedals. So the rear wheel must be as stiff as possible in order not to slip away when transfering the power.
During a lateral stiffness test, a wheel can behave in different ways depending on the load applied on the rim and it’s worth noting that no specialist technical magazines speak about
it.
First of all, the load pulls the rim to the bottom, so the spokes on a side gain tension, and the spokes on the other side lose tension. When the load is low, the stiffness curve of the
wheel stays straight. However, when the load is high, the spokes on the non drive side get totally slack spokes on only one side of the wheel are maintaining wheel integrity.
See the deformation curve below: the curve is straight (stiff wheel) as long as the load does not exceed the moment when the spokes on the non drive side lose their tension (before the point 4). As soon as the load is too high and the spokes have no tension, the curve changes direction and is not as steep. It means the lateral stiffness after the wheel is over-loaded is not as important as when the the wheel is loaded « normally » (the intermittent curve compared to the continuous curve before point 4). That is why it is important to mention the load used on a lateral stiffness test, it reveals which wheel is performant for a certain rider weight/strength, and which wheel will not be as good for the same rider weight/strength.
For example, on the drawing above, the wheel is very stiff up to 18kg loads. It loses its intrinsic stiffness just before the 20kg meaning a heavy rider of more than 90kg, or a slightly lighter but very strong rider putting a significant angle on the bike while standing.
That is why we need to specify the load used to calculate lateral stiffness.
In this test, the load is 20kg.
Before giving the raw results for dozens of wheels, let’s specify a couple of things: the front wheels are stiffer than rear wheels. They are always stiff enough because they are perfectly symetric and have wide bracing angles, and they only have to deal with the rider weight and not transmitting power to the road.
2c) The lateral stiffness – Who does what?
The lateral stiffness of a conventionnal wheel depends on several parameters.
First of all, the rim will determine the stiffness of the wheel by its depth, its torsional stiffness and spoke length.
Then, the spokes give the wheel integrity and play a role in the stiffness according to their tension and their cross section.
Finally, according to Mavic, the most important parameter is the bracing angle, which is the distance between the flanges of the hubs.
Thus, in order to increase the lateral stiffness of a wheel one needs to:
– use a stiff and deep rim which will also comes with shorter spokes
– use larger spokes
– increase the bracing angle: hubs with flanges as far as possible
– high tensioned spokes to delay the moment when the wheel loses all its stiffness (see 2b)
However, all these « improvements » come with a weight penalty so we have to make compromises and identify the improvements with a big impact on stiffness but the smallest weight penalty: deep rim (increasing aero properties too), hubs with widely spaced flanges. Flange diameter will play a role too but it will come with an important weight penalty.
Beside the lateral stiffness of a wheel, the rim movement at the opposite of the spot where the rim is loaded, is important. A high deflection of the rim between the brake pads may slow the rider during the acceleration phase if the rim hits the pads…
The parameters playing a role here are not well known but when digging deep inside the stiffness/deflections at 180° sheet, there are at least two important parameters:
– the rim depth: the shallower it is, the smaller are the deflections between the brake pads, but the lower is the lateral stiffness of the wheel
– the spoking: the higher is the spoke count, the lower are the deflections between the brake pads, and the higher is the wheel stiffness.
Thus, a box section rim with a high spoke count can have two times less deflections between the brake pads, than a wheel with the same construction but a deep rim and a low spoke count!
To quote a few examples: this is the case for the Lightweight Standard G3/Ventoux, the Campagnolo Bora/Hyperon, but also the Shimano C24TU/C50TU, Speedcomposites, Easton EC90 SLX, etc.
The stiffer wheel is the one with the deeper rim, but if you rely on the deflections between the brake pads, this is the inverse…!
That is why it is interesting to use a deep and stiff rim with a high spoke count (at least 24) to benefit from the highest stiffness, and the smallest deflection between the brake pads.
However, this also comes a weight and aerodynamic penalty, so this is best reserved only for rear wheels.
The stiffest wheels are those taking the best of these two characteristics.
There are also different constructions on the market, using different systems and we’ll delve into these below.
The stiffest wheels are those taking the best of these two characteristics.
There are also different constructions on the market, using different systems and we’ll delve into these below.
2d) The lateral stiffness – Results
The results can be found in the table on the left. They are classified in alphabetical order, in two separated columns.
Obviously, the wheelsets featuring the same construction front and rear have their front wheel stiffer than the rear because the bracing angle is wider. There are some special
cases, especially from the biggest manufacturers, where the rear wheels are as stiff or stiffer than the front wheels. This comes from the optimisation of the wheel components:
special spokings, extreme tensions, unusual constructions (Mavic R-SYS for example) You can find in the graphs below the lateral stiffnesses ranked in descending order, for the front and rear wheels.
Front wheels stiffnesses | Rear wheels stiffnesses |
![]() |
![]() |
Click to enlarge | Click to enlarge |
2e) The lateral stiffness – Comments
These graphs highlight the big manufacturers, often offering OEM, whose wheels always reach high lateral stiffness values. Because these giant manufacturers sell to a large population, sometimes light users, sometimes heavy users, their wheels have to offer extreme stiffness which also comes with durability. Indeed, a heavy rider stresses more the wheels than a light rider. If this heavy rider uses a too flexy wheel, it will easily go out of shape while sprinting and its spokes (most of the time the rear wheel non drive side spokes) will often lose their tension. This has three consequences: the wheel will go out of true if the spokes are not locked, the rider will feel the lack of stiffness which is poor for the performance and the spokes will have a shorter working life (and break).
Shimano, Mavic and Campagnolo, the three main players, always have very stiff wheels in their catalog (at least the top end wheels). These wheels are made as a complete system and not as separated components, which comes with advantages and disadvantages.
First, the advantages concern, as mentioned above, the lateral stiffness, but also the durability and the functionning of the components together.
On the downside, some concessions are made: the product is not always adapted to the rider, the components of these wheels are specific and generally can’t be replaced as easily, spoke tensions are always very high which means the components are reinforced and thus heavier. These wheelsets often weight far more than offerings from the more exotic manufacturers.
Indeed, the more exotic manufacturers can use conventionnal construction with standard components. The weight savings are more important here than extreme stiffness. Here we would include Reynolds, Tune, Specialized, FRM, DTSwiss and others.
2f) Special cases
Conventionnal wheel designs have remained unchanged for decades: the rim and hub are held together with spokes and nipples.
However different construction approaches are increasingly available.
1 – The Carbonsports Lightweight have full carbon spokes wrapped around the hub and molded into the rim and the Mavic Cosmic Carbone Ultimate uses this concept too is stiffer with different spoking on the non-drive side of the rear wheel. This kind of construction is very stiff and of course very light too (1200g for the CCU and less than 1100g for the Lightweight), but it is also extremely versatile. The downsides of this approach are that repair is extremely difficult, they are sensitive to crosswinds and expensive.
2 – The Mavic R-SYS uses very stiff tubular carbon spokes at low tension that work in both traction and compression. Lateral stiffness is high despite the shallow and light
rims (1380g per set). These wheels are well suited to climbing because of their stiffness and low weight (for alloy rimmed wheels) and at lower climbing speeds the high drag due to the thick spokes is less of a concern.
3 – the Lew Racing Pro VT-1 have carbon/boron spokes bonded into the rim and the hub, they have no tension so the wheel is extremely flexy laterally and radially. However,
when moving, the rear wheel remains extremely stiff because the power output of the rider passes through the central flange of the hub, which is in the same plane as the rim. This central flange prevents lateral rim movement between the brake pads because the torque passes from the hub to the rim directly.
All other wheels, equipped with a standard dual flange hub, transfer torque with a lateral component created by the bracing angle of the wheel (i.e. paragraph 2b of the lateral stiffness), so the rim is liable to move between the brake pads.
Said another way, the lateral stiffness test represents the deformation of the wheel due to rider weight and rider strength. But, for the Lew, this test does not reflect the dynamic
qualities of the wheel well, it only shows the rider weight limit, because the Lew does not flex a great deal laterally when stomping on the pedals.
Below you’ll find a graph showing theoretical differences in lateral stiffness for four of the most special wheels of the market constructed from our data on rim deflection at two different loads.
We can clearly see that the very small lateral stiffness difference (slope of the curve) under small loads, get much bigger once the rim starts to deflect. The Mavic Cosmic Carbone Ultimate is extremely stiff despite a very low weight (1200g the set), the Lightweight Standard is a little flexier, and the Obermayer, even more so. This is in part what’s prompted CarbonSports to launch a Sprint version of its wheels for 2009, which it claims will restore them to first place again. They use 20 spokes front and 24 rear, versus the usual 20 spokes rear, to achieve this.
The Lew Pro VT1 is pretty stiff under low loads (50N/mm), but it slips away under medium load. This kind of wheel is perfect for light and medium weight riders, but it will offer poor performance for heavier cyclists who will see the wheel deformed, not because of their strength but because of their weight.
The way the wheel deforms is amazing, have a look at this:
In order to support our findings regarding the differences with a very stiff wheel, have a look at these two videos:
Lew wheels video: the spokes bend with the load
Lightweight wheels video, the spokes stay stiff despite the load
Conclusion – Using our data on lateral stiffness to choose the right wheel
The feeling of efficiency and performance on the road mainly comes from the inertia of the wheels (see article n°2 of the Great Wheel Test 2008), but lateral stiffness is important too. A wheel flexing during a hard acceleration and the rim hitting the brake pads results in significant power loss and therefore slower acceleration.
The stiffness of a wheel must be as high as possible to optimise performance under these conditions. However, not every cyclist will benefit from high stiffness. Only heavy and/or very strong cyclists may feel the difference between a wheel whose lateral stiffness is 45N/mm with another one at 55N/mm. Lighter riders and those who just want to enjoy a comfortable ride do not really have to focus on stiffness as an important criterion – inertia is likely to be far more important for them.
It also is not necessary to get the stiffest wheel at all costs because this may compromise other characteristics of the wheel. High lateral stiffness often means a heavier wheel, meaning higher inertia and therefore harder accelerations or more difficult climbs. Ideally, one should choose the wheels with the best weight to stiffness ratio, considering your own weight and it’s important not to forget aerodynamics (see article n°1 of the great wheel test) or bearing resistance (a further article to come soon on this).
Recommendations to optimise racing performance:
Basically, only heavy riders, or racers looking for extreme performance need stiffness at all cost. Over 80kg, the racer should focus on wheels over 40N/mm of lateral stiffness.
Between 70-80kg, wheels under 35N/mm are likely to impair performance in some race situations. And finally, racers between 60 and 70kg would be best avoiding wheels with lateral stiffness
below 30N/mm.
Part 0 – Introduction
Part 1 – Aerodynamics
Part 2 – Inertia
Part 4 – Bearing resistance
Part 5 – Conclusion